|
CALFA BAS is New Generation Water Treatment for cooling tower-cooling system-water chiller to save Water and Energy |
|
 |
|
"CALFA BAS" is water treatment preparation friendly to the Environment, and which Conditioner for the circular cooling system accorded in the ISO14001. "CALFA BAS" is an inorganic product, economical, safe and easy to handle with remarkable effects, replacing the management of the circular cooling water by organic compound chemicals. |
|
 |
|
 |
Term "SCALE" usually is referred to an intimate mixture of sparingly soluble mineral salts.
The formation of calcium carbonate, calcium phosphate, silica, silicate salts, calcium sulfate,
and corrosion products depends on the pH and the temperature of water and the concentrations of
impurities in it. The main factor of scale formation is the concentration of dissolved solids by repeated partial
evaporation of the water. Therefore, even those cooling waters that have little inherent tendency
to scale will eventually become scale-forming, given today's practice of reusing water repeatedly
to minimize its consumption. |
|
Hard water is water that contains cations with a charge of +2, especially Ca2+ and Mg2+. These ions do not pose any health threat, but they can engage in reactions that leave insoluble mineral deposits.
Mineral deposits are formed by ionic reactions resulting in the formation of an insoluble precipitate. For example, when hard water is heated, Ca 2+ ions react with bicarbonate (HCO3 - ) ions to form insoluble calcium carbonate (CaCO3 ), like following. Ca2+ + 2HCO3- ---> CaCO3 + H2O + CO2 As scale builds up, water flow is impeded, and heat exchange rate will be decreased. Hence removing them (Ca/Mg/Si) with such like Hydrochloric Acid more often than appliance parts and pipes must be replaced. As you know, Strong Acid Chemicals such " Hydrochloric Acid BASE" makes serious damage to pipes or plant systems.
|
|
|
|
 |
|
Explaining simply with the most common Heat Exchanger "U- Shell & Tube". (Left Pic.) One set of these tubes that made by copper contains the water from cooling tower that must cool.
Although coolant gas flows through the outside of "Tubes of heat exchanger" with high temperature, it liquefies the gas from which heat was taken is left from a heat exchanger as liquid.
At the same time, The water of cooling tower returns to a cooling tower again for decreasing the own temperature after decreasing the temperature of coolant gas.
then, there are 3 factors of thermal resistance to do this inside a heat exchanger.
(1) . Oil Film
(2) . Tube (Copper etc.)
(3) . The scale cooling water makes (Ca,Si formated etc.)
The serious problem is (3),
if scale becomes thick, The capability of heat exchange will be fell down drastically, and cannot liquefy coolant gas completely, be remaining as "Foul Gas" inside it.
If the thickness of scale would become 0.5mm in Tubes of Heat Exchanger, The power consumption will be risen up +60% (160%).
Also while scale would be gradually accumulating from "0mm" to "0.5mm", it used an excess power (electricity) which should not have been consumed.
Scale 0.1mm = (about 110% of power consumption)
Scale 0.3mm = (about 130% of power consumption)
and, Even if the thickness of scale is the same , the thermal conductivity of "Silica Scale" is TWICE lower than Calcium scale. Therefore, The most Key point to save an energy is how to remove & prevent "Silica Scale" inside it.
Thermal conductivity :
(Copper 400 W/mK, Calcium 0.6 W/mK, Silica 0.3 W/mK)
|
|
|
 |
The most common way to soften water is by using of an ion exchange water softener. This device uses an ion exchange process to replace hardness minerals (Ca & Mg) in the water with another substance. Most water softening equipments today use sodium for this exchange. The process consists of flowing the hard water over a bed of plastic resin beads. On each bead, slight electric charges hold sodium ions on the surface of the bead. As hard water flows through the water softener, it passes around the plastic beads. The hardness minerals (ions) in the water have a greater attraction to the bead than the sodium on the bead. Therefore, they attach themselves to the bead, and in the process they displace the sodium ions (Thus the name ion exchange). It's really effective for Ca and Mg, however, SILICA(Si) is easy to pass a water softener device because it does not exchange ion on this process perfectly. It needs some very expensive equipment facilities if you would like to remove silica in the water perfectly. As a result, most of problem facilities have is making SILICA Scale all over the world. However, please note that the BEST advantage of "CALFA BAS" is to remove SILICA scale just only install CALFA BAS to a bottom of cooling towers. It also keeps effective for 6 months(*) long. Of course It's not necessary to place metering units, chemical drums either. |
(*) 12hours cooling system working / Per day |
|
|
 |
Silica scale formation is a serious problem with cooling water that has high dissolved silica content, such as sea water. Silica and/or magnesium silicate deposition limits industrial water users to low cycles of operation. In certain regions water used for industrial cooling contains "high" concentrations of silica. Silica's solubility depends on the dissolved species and temperature. This difference imposes severe limits on water users and forces them to take either of 4 Approaches.
1. |
Operate at very low cycles of concentration (thus consuming enormous amounts of water, cost huge expensive) |
2. |
Chemically treat the cooling water to prevent silica scale formation and deposition with complicated mixture
"Organic Compound Chemicals". (thus cost expensive, polluting air, destroying environment ,and generating red tide, etc.) |
3. |
Acid Washing periodically with " Hydrochloric Acid" such like based on Strong Acid.
(thus cost expensive, damages to your system ,and danger for workers,etc. ) |
4. |
Just immerse "CALFA BAS" in your cooling towers (Environmentally friendly, Absolutely Safe, Reasonable Cost) |
|
|
|
|
The needed fuel will increase drastically even if scale will be fouled a little, because of the thermal conductivity of scale are quite smaller than steel pipes so.
Right Graph shows the thickness , kinds of fouled scale ,and the increased rate of the amount of fuel using in BOILER case.
As you can see, about 3 TIMES of fuel is needed,
though SILICA scale fouled is even same thickness with CALCIUM scale. If the scale is foulded, the need of fuel increase, besides, the flow resistance in pipes goes up because of a decrease in the rate of Water. So water would not enough circulate smoothly. Finally, pipes may be burst by evaporation.
The SILICA problem bothers the person in charge of maintaining cooling towers or water chillers in the world. You will be surprised that CALFA BAS's preeminent capability for the silica scale removal, and your stereotype will be changed when you use CALFA BAS one day. |
|
|
 |
|
|
|
Like as above a graph, Scale are fouling gradually until Acid Washing will be done once a year. While scale will be fouling a little by little, the excess energy are spent a little by little as well. That is to say, You are spending much more energy which you don't need to spend even while not noticing. On the other hand, You just only install CALFA BAS (blue line) at the bottom of a cooling towers, It will not foul scale anymore. So, you can always use your system 100% capability. How much difference and profit you can make
if this big cost is included ? You can try ,and know from your bill of Electric Company! |
|
|
|
Until 20th century, It was a common way of maintenance to resolve a problem of scale formation using "2Hcl" (
Hydrochloric Acid
) in order to melt "Ca", "Mg", "Fe" etc. as an acid detergent, "NH4HF2" (Ammonium Fluoride) for Silica, and "NaHO" (
Sodiu-
m Hydroxide)
as neutralization chemical, but this method has several big problems. Environmental deterioration and pollution,
Danger to Human Bodies and Health because of Hazardous Chemicals, Cost Expensive,
Damage to system and facilities,
Collecting wastewater and so on. The 21st century has started ,and the environmental preservation and global warming has become a major problem all over the world rapidly. |
|
|
|
|
|
 |
|
 |
As you can see, Right Graph is a sample of the cost comparison of doing "Acid Washing once a year", with installing "CALFA BAS" while cooling system is operating. This graph shows just the difference of "Chemical Cost" which is not including the save water cost, and the energy cost.
If your cooling towers operate only for "Air Conditioners" in Summer season, The difference would be expanded. Because "CALFA BAS" does not need to be installed while a cooling system is not operating in winter season as you know.
Moreover, It contributes to save your energy, and then in proportion as CALFA BAS use, the cost merit will be bigger. Of course it makes a large contribution toward keeping environme-ent. |
|
|
It's a big responsibility to have the person in charge who will not use it will keeps spending the excess water and energy , then waste much money of your company for a long time in spite of meeting "CALFA BAS" now. |
|
 |
|
|
When cooling towers contain an open recirculation system, microorganisms can spread from air to water. Microorganisms can rapidly multiply, when a substrate is present and a number of conditions are ideal for microbial growth. ex. Temp. , Oxgen & Nutrient concentration in water. The nutrient content increases, because of water evaporation.
Bacteria grow up with nitrogen(N) ,and change to BIOFILM step by step.
The difference is "SPEED" of growing up as compared with Scale case.
3-4 days are enough to be "1mm" in summer season.
If your cooling towers are located near agriculture fields, food factories, organic chemistry factories, the sea, and main streets congested with traffic, the Nitrogen level in water of your cooling towers goes up easily. Moreover, it is easy to grow the number of bacteria up by the latest climate change. (warmer) If you would like to always count "0" the number of bacteria, |
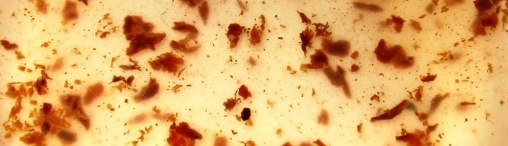 |
|
We would to recommend using "CALFA BAS" and "CALFA SAT" together. |
|
|
If the thickness of scale would become "1.2mm" in Tubes of Heat Exchanger, The power consumption will be risen up +25% (125%).
Most of cases, Slime contains scale (Ca, Mg, Si etc.) mixed and fouled any pipes, heat exchangers, inside cooling towers.
Therefore, We usually install CALFA SAT (Bactericide) 7 - 10 days earlier than CALFA BAS install, because It's better to take "Time Lag" for removing Slime & Scale. Removing any Bacteria using CALFA SAT only first 10 days. then, keep using CALFA SAT , install CALFA BAS. |
|
|
|
|
|
BIOFILM mixed MUD (It almost all blocked) |
|
|
Above pictures are heat exchangers of a factory which is located to an industrial area near the sea. It's always windy strongly, and the nitrogen level of water is usually high. Slime and Sand were mixed and fouled, finally, holes of the heat exchanger had been plugged up. It caused the heat exchanger HIGH CUT , and the production line was stopped. That was serious heavy losses for them. It is typical case that "prevention" is the most important to operate production lines without any loss. |
|
|
|
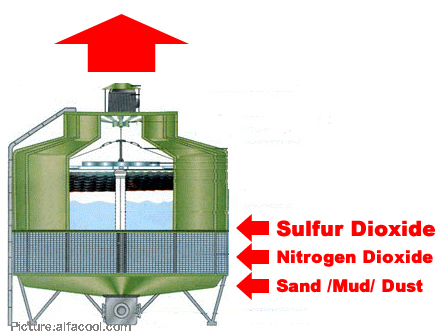 |
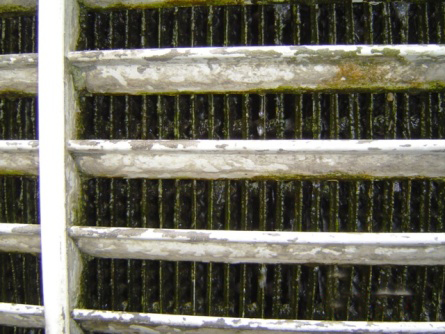 |
The source of the Bacteria trouble
|
ALGAE |
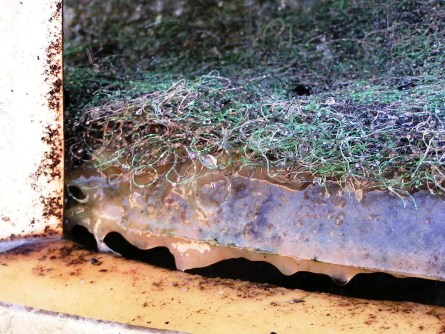 |
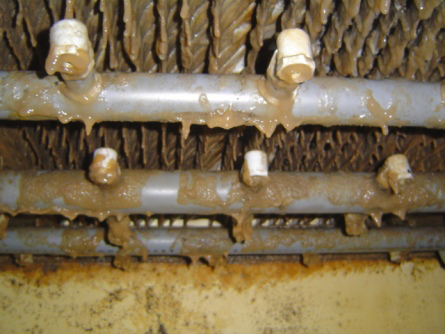 |
SLIME |
SLIME |
|
Some sticky substance (Slime, BIO Film) is not made in cooling towers with using "CALFA BAS" and "CALFA SAT" together. As a result, sand, mud, dust, are not mixed into it,
If those kinds of slime or algae problem would bother you, please use "CALFA BAS" and "CALFA SAT" together. It comes "PERFECT COMBINATION" more powerfully. |
|
|
|
.png) |
|
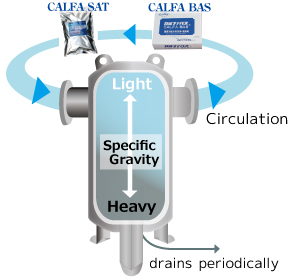 |
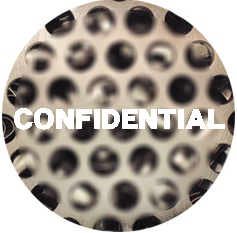 |
There are wide variety of "Water Separators" available in the marketplace of the world.
However, The Water Separators which named "S.E.P." has "Special Unique shape of RINGs" inside of it. The Special Unique shape of RINGs is possible to separate till 7-micron impurities (minimum). Plus, using with an agglutination reaction of CALFA BAS together, Materials of increasing Specific Conductivity such as calcium magnesium silica, iron, etc. in the circulation water remove and decrease to 10% for few days.
It does not need to replace RINGs for few years like a "Sand Filters". NO Backwash, NO PAC (polyaluminum chloride), but gives you Bigger Water Saving ! |
|
|
|
|
|
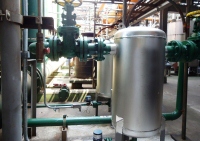 |
An Major Iron Factory's case
(Using in SIDE FLOW Filtration)
just replaced as sand filtrers that was previously used. |
Big Sand Filters (2UNITS) replaced to CALFA S.E.P. (2UNITS) |
(Water Analysis for 20 days) - 24Hours operating - |
2011.9.16 Total Hardness:892mg/L Tubidity:135(NTU) -START-
2011.9.19 Total Hardness:607mg/L Tubidity:76.1(NTU)
2011.9.20 Total Hardness:510mg/L Tubidity:61.8(NTU)
2011.9.21 Total Hardness:419mg/L Tubidity:51.8(NTU)
2011.9.22 Total Hardness:410mg/L Tubidity:48.1(NTU)
2011.9.23 Total Hardness:409mg/L Tubidity:41.8(NTU)
2011.10.03 Total Hardness:398mg/L Tubidity:22.1(NTU)
2011.10.04 Total Hardness:369mg/L Tubidity:19.2(NTU)
2011.10.05 Total Hardness:359mg/L Tubidity:18.3(NTU)
(60% Down !! ) (87% Down !! ) |
|
|
|
|
|
 |
|
, |
|
|
 |